
"Machiavelli" was designed during Summer 2021 and flown 9/19/2021 at CRMRC near Lake Champlain, Vermont. It reached an apogee of 6381ft AGL on an Aerotech I327-DM with a flight time of 48 seconds. The rocket is a 38mm "minimum diameter" and stands 5ft tall. Onboard electronics include an Eggfinder GPS/900MHz radio in the nose, 2x Stratologger dual-deploy altimeters, and a Runcam Split for onboard video. This project pushed my design and packaging skills to fit everything into such a small space, pushed the boundaries of 3d printing in model rocketry, and went more than 3x higher than my previous rocket, Bobby Tables.
During the first flight, the drogue section failed to separate and the main parachute's swivel snapped during main deploy. Both drogue ematches were fired, so the most likely cause of this failure is poor drogue bay sealing. Graphs and pictures from that flight are below.
On its second flight, Machiavelli broke apart at around Mach 1 flying on a J500G. The exact failure mode is unknown. Half of the electronics bay (containing the two altimeters) and GPS was recovered -- the motor casing, camera and batteries were lost. More pictures are below the first flight at the bottom.
Above: Flight 1
Below: Flight 2

Machiavelli being weighed in flight configuration. Separation points are located between motor section and Avionics bay, and upper section to nosecone

Machiavelli in Solidworks

OpenRocket model, used to verify stability and simulate the flight

Simulation data from OpenRocket on an I327-DM. We'll compare this to our actual flight data at the end

Machiavelli's electronics bay in CAD. There's barely any space left unused!

Machiavelli's electronics bay in real life. Black powder is packed into the wells on the left and right to deploy parachutes


Machiavelli's nosecone GPS tracker + radio in real life (left) and CAD (right). The Eggtimer Rocketry "Eggfinder" was soldered and assembled by me.
The rocket made heavy use of 3d printed parts - even the fins were 3d printed! Parts were printed out of Markforged Onyx, which is flexible and tough. As we'll see at the end, those fins took a fall at over 100ft/sec without a scratch.


Load testing the fin can

Machiavelli's airframe was constructed from 38mm Blue Tube and spray painted

Gluing the 3d-printed fincan to the motor section
Flight 1 results
The boost phase of the first flight went well, though we lost sight of the rocket shortly after launch. The main parachute and its Nomex protector were recovered shortly after launch, though with no rocket attached. The rest of the rocket was recovered after we reacquired radio and got GPS packets. The motor section and avionics bay were recovered sitting ~100ft from the nosecone tracker, which had been ripped off of its shock cord by splitting the 3d printed mount along layer lines. Main deployment appeared to have also ripped its shock cord clean though the main parachute section up to its bulkhead. No exact failure mode is known, but I suspect poor sealing between avionics bay and the middle airframe section lead to insufficient pressure to push the main out.

Main parachute and Nomex protector. Note the sheared swivel and torn Nomex blanket
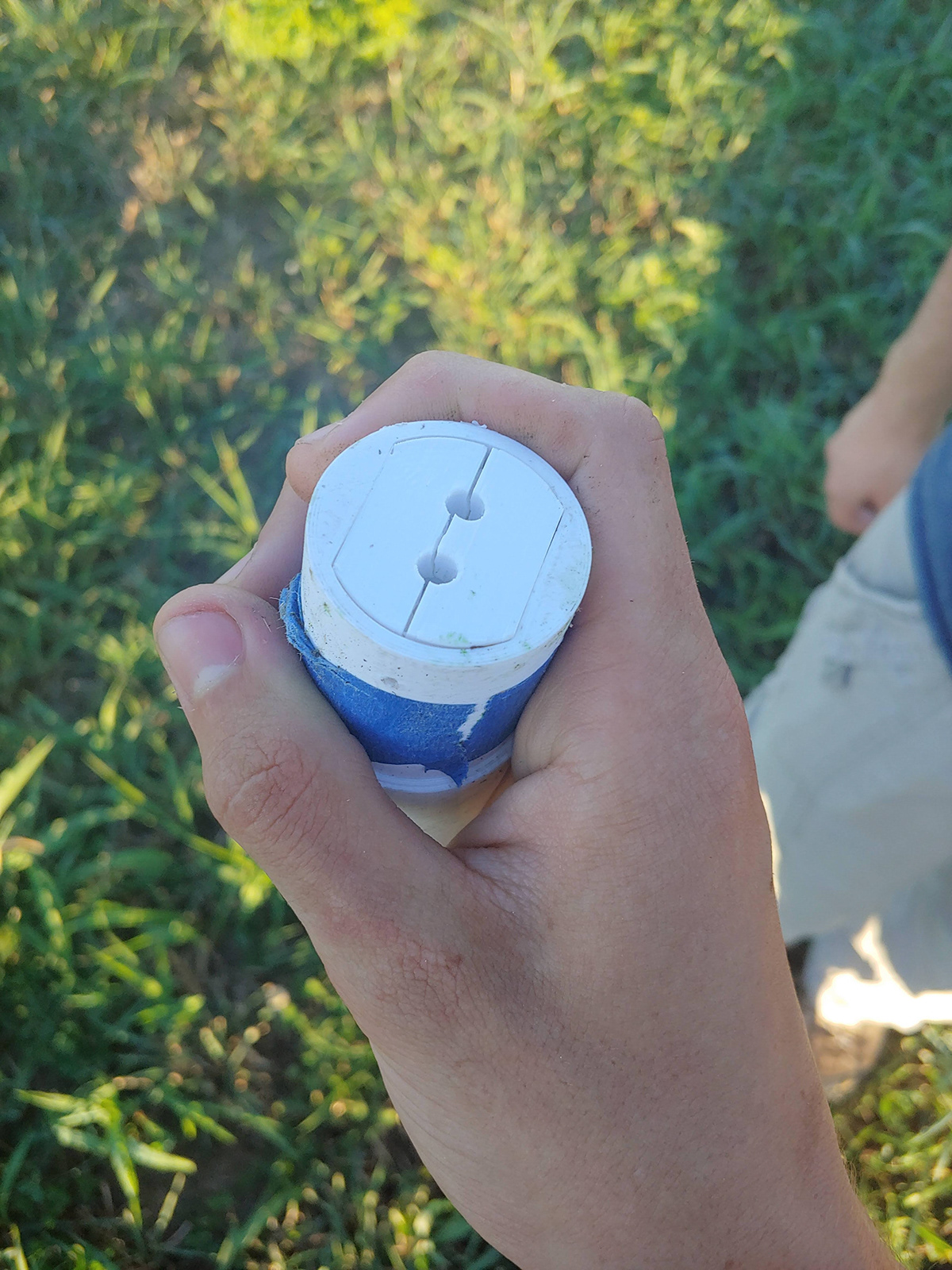
Nosecone+GPS, torn from its shock cord mount

Avionics bay and motor section (above)
Main parachute shock cord damage (below)


The flight of the rocket was visualized using Google Earth. Contact was lost with the GPS ~40 seconds after launch, which is consistent with it hitting the ground. GPS data and altimeter altitude data were fused in the second image below to produce an approximate 3d visualization of the flight.



Flight data indicates no drogue came out at apogee
I learned a lot from this flight about what works and what doesn't. For the next flight, I mounted the nosecone shock cord on a bolt so we aren't loading a 3d print along its layers, didn't use a swivel that can shear, and used more robust sealing around the drogue bay to increase deployment reliability.
Flight 2 Results
The Stratologger altimeters came umplugged when the rocket broke up, but continued running for 2 seconds. Below is shown the data (left) as well as the OpenRocket simulation (right). The data suggests the rocket broke up around Mach 1. The exact failure mode is unknown, but there were a few factors which could have compounded.
- The fit between sections was poor, meaning the top of the rocket could wobble about the motor section
- The rocket was long/skinny and had lots of mass forward
- The fins were small compared the overall rocket (?)
- Large camera hole created a stress concentration in the body tube
- Shear pin placed slightly too high meant the upper section could have transferred thrust loading through shear pin rather than through body tube walls
Future rockets will seek to remedy these issues by doing the following:
- Avoiding long/skinny rockets with long poor-fitting sections (make the rocket fatter, use tighter tolerance materials, or place couplers closer to the electronics bay to reduce moments about the coupler)
- Avoiding large camera holes in small rockets
- Avoiding non-conventional avionics bays except where necessary


The remains of Machiavelli's electronics bay